New Launch Racks

Quote from Admin on December 7, 2024, 6:09 pmOver the past few months, we've had more and more newcomers to our launches. As expected, these newcomers don't come out to launch big rockets, save for, perhaps, the ARC team kids, so our 1/8th inch and 3/16th inch racks have been in high demand. I took it upon myself to build two more racks of rods.
As many of you know, the existing racks have been around for some time. They predate my time with CENJARS, so I don't know who originally built them. Charlie replaced the metal sawhorse that these racks were seated upon a couple of years ago with a wooden sawhorse. The pads were built using marine antenna mounts to allow a pan and tilt feature for each rod. The problem has been that the tilt can not be finely tuned due to ratchet teeth on the adjustments. I did bring and install some large neoprene washers (like fender washers) in between the teeth on one of the racks at a recent launch which helped to make finer adjustments a reality. However, the pan capability does not have a simple quick adjustment.
I've seen this as a weakness for a long time. While many clubs have multiple launch racks, most do not have a pan and tilt mechanism; only straight up rods. I like that our members can have some freedom to adjust the initial trajectory of their rockets. Because of this, I sat down and designed a simpler pan and tilt gimbal for a new launch rack. This Gimbal — actually twelve of them — has been 3D printed. This is an engineering drawing from my 3D design software for your perusal.
Here is an exploded virtualization rendering view of a Gimbal from my 3D design software.
The entire Gimbal assembly can be panned by turning the assembly via the ridged ring at its base. The pan is dampened and holds its place via a set of specialized cushioning washers. There is a stop integrated into this pan mechanism to allow a ±20º panning extent.
The tilt mechanism of the Gimbal is controlled by releasing and tightening a four-arm knob on the side of the Gimbal. This knob does NOT need to be torqued tightly to hold the rod at the user's desired angle. Also, to adhere to the NAR's safety code restriction of 20º maximum launch angle, there are stops in the tilt mechanism enforcing it.
The Gimbal will accept both 1/8th inch and 3/16th inch rods. The rods are held in place with a thumb screw. This makes setup of the pads much easier.
The blast deflectors are repurposed 5½inch diameter heavy-duty stainless-steel food service plates. These are available for ~$5 each which is cheaper in price than the blast deflector plates sold by Estes. In addition, I created some aluminum standoffs with thumbscrews to replace the clothespins we've been using. The only drawback to these is that the occasional minimal diameter rocket might have its motor ignitors touching and shorting on these standoffs. Nothing a simple piece of masking tape can not remedy.
If you'd attended the December 2024 launch, I had one of these launch rails on display.
One of the other design features I have incorporated in the new launch raise is a casing system. There is a box which encloses the launch rack and Gimbals to protect them in transit. When the case is opened, one side maintains large bold numbers denoting each pad relative to the rack. The launch rods are maintained within the case when closed. Each rack is 48 inches 4 feet) in length which should mean that most any member of the club should be able to transport these racks in a typical automobile trunk.
Pictured below is another design software rendering of the launch racks. I made one rack red and the other rack blue. This is intentional to coincide with the new launch controller I've been working on. I'd really hoped to have it completed this past year but surgery, and the health and death of my father-in-law tossed a spanner into those plans. There's another thread in this forum about the launch controller you can peruse if you've not seen what's in the works.
Over the past few months, we've had more and more newcomers to our launches. As expected, these newcomers don't come out to launch big rockets, save for, perhaps, the ARC team kids, so our 1/8th inch and 3/16th inch racks have been in high demand. I took it upon myself to build two more racks of rods.
As many of you know, the existing racks have been around for some time. They predate my time with CENJARS, so I don't know who originally built them. Charlie replaced the metal sawhorse that these racks were seated upon a couple of years ago with a wooden sawhorse. The pads were built using marine antenna mounts to allow a pan and tilt feature for each rod. The problem has been that the tilt can not be finely tuned due to ratchet teeth on the adjustments. I did bring and install some large neoprene washers (like fender washers) in between the teeth on one of the racks at a recent launch which helped to make finer adjustments a reality. However, the pan capability does not have a simple quick adjustment.
I've seen this as a weakness for a long time. While many clubs have multiple launch racks, most do not have a pan and tilt mechanism; only straight up rods. I like that our members can have some freedom to adjust the initial trajectory of their rockets. Because of this, I sat down and designed a simpler pan and tilt gimbal for a new launch rack. This Gimbal — actually twelve of them — has been 3D printed. This is an engineering drawing from my 3D design software for your perusal.
Here is an exploded virtualization rendering view of a Gimbal from my 3D design software.
The entire Gimbal assembly can be panned by turning the assembly via the ridged ring at its base. The pan is dampened and holds its place via a set of specialized cushioning washers. There is a stop integrated into this pan mechanism to allow a ±20º panning extent.
The tilt mechanism of the Gimbal is controlled by releasing and tightening a four-arm knob on the side of the Gimbal. This knob does NOT need to be torqued tightly to hold the rod at the user's desired angle. Also, to adhere to the NAR's safety code restriction of 20º maximum launch angle, there are stops in the tilt mechanism enforcing it.
The Gimbal will accept both 1/8th inch and 3/16th inch rods. The rods are held in place with a thumb screw. This makes setup of the pads much easier.
The blast deflectors are repurposed 5½inch diameter heavy-duty stainless-steel food service plates. These are available for ~$5 each which is cheaper in price than the blast deflector plates sold by Estes. In addition, I created some aluminum standoffs with thumbscrews to replace the clothespins we've been using. The only drawback to these is that the occasional minimal diameter rocket might have its motor ignitors touching and shorting on these standoffs. Nothing a simple piece of masking tape can not remedy.
If you'd attended the December 2024 launch, I had one of these launch rails on display.
One of the other design features I have incorporated in the new launch raise is a casing system. There is a box which encloses the launch rack and Gimbals to protect them in transit. When the case is opened, one side maintains large bold numbers denoting each pad relative to the rack. The launch rods are maintained within the case when closed. Each rack is 48 inches 4 feet) in length which should mean that most any member of the club should be able to transport these racks in a typical automobile trunk.
Pictured below is another design software rendering of the launch racks. I made one rack red and the other rack blue. This is intentional to coincide with the new launch controller I've been working on. I'd really hoped to have it completed this past year but surgery, and the health and death of my father-in-law tossed a spanner into those plans. There's another thread in this forum about the launch controller you can peruse if you've not seen what's in the works.
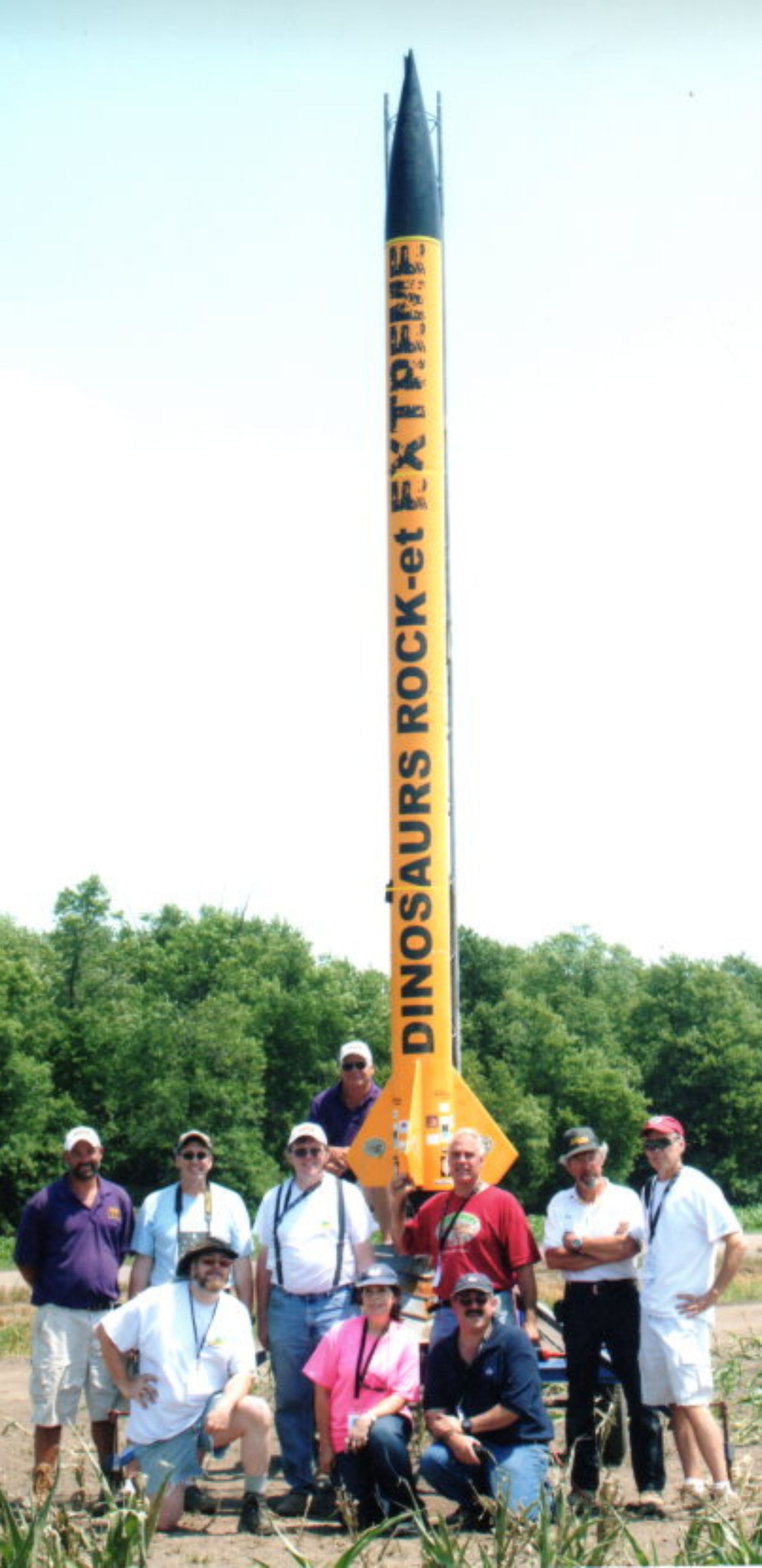

Quote from Ckirlew on December 8, 2024, 10:05 amOverall, the racks are great. Very professional looking. As the equipment manager, I look at 3 basic areas: storage, transportation (to the field and on the field), and use. I haven't had much interaction with them so this is based on mostly visual information.
Storage: They close up nicely and don't have things poking out of them like the handles on the current racks. I haven't looked at how the legs work. The current ones are a little persnickety. Once you get to know how they work they're ok, but the legs do stick out a bit. New racks look like they are far more stream lined. Not sure how the legs stay open or closed.
Transportation: One of my main concerns here is weight. I don't want anyone (especially me) hurting their back getting stuff in and out of the van. Storing the rods in the rack sounds nice but I want to look at that some more. It does add weight to the whole package. The existing storage tubes adds the flexibility of having space for extra rods. Getting them from the van to the launch area shouldn't be an issue since they are sleeker. The casing enclosure adds some weight but is probably worth it. The deflector shields should eliminate the flower pots, reducing expense from breakage and ease the setup process. I think setting them up convex would be better than concave. Also would add to the length of the usable rod.
Use: One of the "ingenious" things I did with the existing racks was color code the rods by size. It wasn't easy to see and you had to know to look for the different colors to know the size. Is there a way we can easily mark the new racks with the size of the rod (1/8 or 3/16)? We need something to hold the wires on the rack. The holders on the current racks should be transferable and I have a few extras.
The standoffs are a nice feature but being conductive isn't good. We did have one failure early on Sunday where there was contact across the standoff. Brian mentioned something about anodizing them. If it works, great. How long does the anodizing last? Also, there probably wouldn't be an issue with the motor hooks getting caught on them. Downside is I often use the clothespins to hold the wire clips apart. The dog bones that Brian made several months ago are ok but a little restrictive. Maybe a new design, larger, something?
I added some holes to the legs of the current stand so they could be spiked down when we had gusty winds. Is there any way to add some stability like that to these stands? The foldup casing looks great but adds to the surface area of the rack.
Numbering system? I understand a color code for the pads. I would prefer not to announce "On pad Blue 2" or "On Red 1". I know they need to be coordinated with the controller. Just wondering if it's too late to change the design on that aspect of the complete system.
That all I have for now. Again, I haven't played with the new racks much at all. I am looking forward to it.
Charlie
Overall, the racks are great. Very professional looking. As the equipment manager, I look at 3 basic areas: storage, transportation (to the field and on the field), and use. I haven't had much interaction with them so this is based on mostly visual information.
Storage: They close up nicely and don't have things poking out of them like the handles on the current racks. I haven't looked at how the legs work. The current ones are a little persnickety. Once you get to know how they work they're ok, but the legs do stick out a bit. New racks look like they are far more stream lined. Not sure how the legs stay open or closed.
Transportation: One of my main concerns here is weight. I don't want anyone (especially me) hurting their back getting stuff in and out of the van. Storing the rods in the rack sounds nice but I want to look at that some more. It does add weight to the whole package. The existing storage tubes adds the flexibility of having space for extra rods. Getting them from the van to the launch area shouldn't be an issue since they are sleeker. The casing enclosure adds some weight but is probably worth it. The deflector shields should eliminate the flower pots, reducing expense from breakage and ease the setup process. I think setting them up convex would be better than concave. Also would add to the length of the usable rod.
Use: One of the "ingenious" things I did with the existing racks was color code the rods by size. It wasn't easy to see and you had to know to look for the different colors to know the size. Is there a way we can easily mark the new racks with the size of the rod (1/8 or 3/16)? We need something to hold the wires on the rack. The holders on the current racks should be transferable and I have a few extras.
The standoffs are a nice feature but being conductive isn't good. We did have one failure early on Sunday where there was contact across the standoff. Brian mentioned something about anodizing them. If it works, great. How long does the anodizing last? Also, there probably wouldn't be an issue with the motor hooks getting caught on them. Downside is I often use the clothespins to hold the wire clips apart. The dog bones that Brian made several months ago are ok but a little restrictive. Maybe a new design, larger, something?
I added some holes to the legs of the current stand so they could be spiked down when we had gusty winds. Is there any way to add some stability like that to these stands? The foldup casing looks great but adds to the surface area of the rack.
Numbering system? I understand a color code for the pads. I would prefer not to announce "On pad Blue 2" or "On Red 1". I know they need to be coordinated with the controller. Just wondering if it's too late to change the design on that aspect of the complete system.
That all I have for now. Again, I haven't played with the new racks much at all. I am looking forward to it.
Charlie

Quote from Admin on December 8, 2024, 6:23 pmQuote from Ckirlew on December 8, 2024, 10:05 amOverall, the racks are great. Very professional looking. As the equipment manager, I look at 3 basic areas: storage, transportation (to the field and on the field), and use. I haven't had much interaction with them so this is based on mostly visual information.
Storage: They close up nicely and don't have things poking out of them like the handles on the current racks. I haven't looked at how the legs work. The current ones are a little persnickety. Once you get to know how they work they're ok, but the legs do stick out a bit. New racks look like they are far more stream lined. Not sure how the legs stay open or closed.
The pads sit atop a steel "sawhorse' framework with retractable legs. There's a steel spring-loaded lock button on each leg. When the legs are pulled down they lock in place. To store them, simply push on the button to fold the leg. Those buttons are the small chrome spots seen in the image below.
Transportation: One of my main concerns here is weight. I don't want anyone (especially me) hurting their back getting stuff in and out of the van. Storing the rods in the rack sounds nice but I want to look at that some more. It does add weight to the whole package. The existing storage tubes adds the flexibility of having space for extra rods. Getting them from the van to the launch area shouldn't be an issue since they are sleeker. The casing enclosure adds some weight but is probably worth it. The deflector shields should eliminate the flower pots, reducing expense from breakage and ease the setup process. I think setting them up convex would be better than concave. Also would add to the length of the usable rod.
I weighed the unit and it is 10.5kgs or 23lbs. As each has a carrying handle position at the CG of each stored pad, this shouldn't be too much to pick up and carry out to the field. In fact, I'd prefer it that way. Also, the units are 48 inches in length which should fit easily in the trunk space of most cars on the American roadways. My concert too was not having things protrude that might damage someone's vehicle if they had to transport them.
Use: One of the "ingenious" things I did with the existing racks was color code the rods by size. It wasn't easy to see and you had to know to look for the different colors to know the size. Is there a way we can easily mark the new racks with the size of the rod (1/8 or 3/16)? We need something to hold the wires on the rack. The holders on the current racks should be transferable and I have a few extras.
Each of the Gimbals is capable of either a 1/8th inch or 3/16th inch rods. The black thumbscrew is used to secure each rod and is independent of the rod diameter. Each rod is held quite securely and the entire rack can be lifted from a rod as I demonstrated at the Tree Lighting. I'd no suggest doing that but it does demonstrate the holding power.
The standoffs are a nice feature but being conductive isn't good. We did have one failure early on Sunday where there was contact across the standoff. Brian mentioned something about anodizing them. If it works, great. How long does the anodizing last? Also, there probably wouldn't be an issue with the motor hooks getting caught on them. Downside is I often use the clothespins to hold the wire clips apart. The dog bones that Brian made several months ago are ok but a little restrictive. Maybe a new design, larger, something?
Not as bas as the stupid Estes motor retainers getting hung up in the clothespin springs. Each rod stop is 3.9mm wider than the rod. If there's an issue with shorting, a simple piece of tape will remedy that. Each thumbscrew is 10-32. I chose that to insure that there would be ample thread in each stop.
I added some holes to the legs of the current stand so they could be spiked down when we had gusty winds. Is there any way to add some stability like that to these stands? The foldup casing looks great but adds to the surface area of the rack.
That should not be necessary. There's ample mass downward to hold the rack in place.
Numbering system? I understand a color code for the pads. I would prefer not to announce "On pad Blue 2" or "On Red 1". I know they need to be coordinated with the controller. Just wondering if it's too late to change the design on that aspect of the complete system.
Many of the larger rocket festivals multiplex pads. MDRA uses a black and red scheme. The launch controller in production has already been CNC cut, laser etched and the PCBs for the inner working have been produced and populated with components. The only real work needed is the main PCB board.
The color coding was selected to simplify and accelerate the setup on the field. I thing we wast too too much time setting up and I'm hoping to shorten the setup time.
That all I have for now. Again, I haven't played with the new racks much at all. I am looking forward to it.
As for cable retainers, there will be magnetic cable restraints.
FWIW, if there's a demand for yet another rack system, I can quickly and easily make another. It'll be green.
Well, quickly might not be the appropriate adjective as it takes about 12 hours to 3D print each Gimbal assembly.
Quote from Ckirlew on December 8, 2024, 10:05 amOverall, the racks are great. Very professional looking. As the equipment manager, I look at 3 basic areas: storage, transportation (to the field and on the field), and use. I haven't had much interaction with them so this is based on mostly visual information.
Storage: They close up nicely and don't have things poking out of them like the handles on the current racks. I haven't looked at how the legs work. The current ones are a little persnickety. Once you get to know how they work they're ok, but the legs do stick out a bit. New racks look like they are far more stream lined. Not sure how the legs stay open or closed.
The pads sit atop a steel "sawhorse' framework with retractable legs. There's a steel spring-loaded lock button on each leg. When the legs are pulled down they lock in place. To store them, simply push on the button to fold the leg. Those buttons are the small chrome spots seen in the image below.
Transportation: One of my main concerns here is weight. I don't want anyone (especially me) hurting their back getting stuff in and out of the van. Storing the rods in the rack sounds nice but I want to look at that some more. It does add weight to the whole package. The existing storage tubes adds the flexibility of having space for extra rods. Getting them from the van to the launch area shouldn't be an issue since they are sleeker. The casing enclosure adds some weight but is probably worth it. The deflector shields should eliminate the flower pots, reducing expense from breakage and ease the setup process. I think setting them up convex would be better than concave. Also would add to the length of the usable rod.
I weighed the unit and it is 10.5kgs or 23lbs. As each has a carrying handle position at the CG of each stored pad, this shouldn't be too much to pick up and carry out to the field. In fact, I'd prefer it that way. Also, the units are 48 inches in length which should fit easily in the trunk space of most cars on the American roadways. My concert too was not having things protrude that might damage someone's vehicle if they had to transport them.
Use: One of the "ingenious" things I did with the existing racks was color code the rods by size. It wasn't easy to see and you had to know to look for the different colors to know the size. Is there a way we can easily mark the new racks with the size of the rod (1/8 or 3/16)? We need something to hold the wires on the rack. The holders on the current racks should be transferable and I have a few extras.
Each of the Gimbals is capable of either a 1/8th inch or 3/16th inch rods. The black thumbscrew is used to secure each rod and is independent of the rod diameter. Each rod is held quite securely and the entire rack can be lifted from a rod as I demonstrated at the Tree Lighting. I'd no suggest doing that but it does demonstrate the holding power.
The standoffs are a nice feature but being conductive isn't good. We did have one failure early on Sunday where there was contact across the standoff. Brian mentioned something about anodizing them. If it works, great. How long does the anodizing last? Also, there probably wouldn't be an issue with the motor hooks getting caught on them. Downside is I often use the clothespins to hold the wire clips apart. The dog bones that Brian made several months ago are ok but a little restrictive. Maybe a new design, larger, something?
Not as bas as the stupid Estes motor retainers getting hung up in the clothespin springs. Each rod stop is 3.9mm wider than the rod. If there's an issue with shorting, a simple piece of tape will remedy that. Each thumbscrew is 10-32. I chose that to insure that there would be ample thread in each stop.
I added some holes to the legs of the current stand so they could be spiked down when we had gusty winds. Is there any way to add some stability like that to these stands? The foldup casing looks great but adds to the surface area of the rack.
That should not be necessary. There's ample mass downward to hold the rack in place.
Numbering system? I understand a color code for the pads. I would prefer not to announce "On pad Blue 2" or "On Red 1". I know they need to be coordinated with the controller. Just wondering if it's too late to change the design on that aspect of the complete system.
Many of the larger rocket festivals multiplex pads. MDRA uses a black and red scheme. The launch controller in production has already been CNC cut, laser etched and the PCBs for the inner working have been produced and populated with components. The only real work needed is the main PCB board.
The color coding was selected to simplify and accelerate the setup on the field. I thing we wast too too much time setting up and I'm hoping to shorten the setup time.
That all I have for now. Again, I haven't played with the new racks much at all. I am looking forward to it.
As for cable retainers, there will be magnetic cable restraints.
FWIW, if there's a demand for yet another rack system, I can quickly and easily make another. It'll be green. Well, quickly might not be the appropriate adjective as it takes about 12 hours to 3D print each Gimbal assembly.

Quote from Eric Becher on December 8, 2024, 8:22 pmNothing is perfect, but the racks seem pretty good. The pie plates need to be upside down. Charlie's concerns are valid, but we can work out or around most of them once they are in service. I do foresee using some clothes pins now and then for various reasons, but we'll see once they are in service. The bones are nice, but they get lost and occasionally just don't fit the situation.
Are the numbers already printed on the controller? We could keep the colors and still number them 1-6 red, 7-12 blue, 13-18 green, etc. But if the etching included numbers already, I wouldn't feel the need to say the color every time. I'd say something like "Moving to the blue rack, on 1, 2, 3..."
For rod size, could we add a label somewhere on the back side of the rack? A rotating disk with 1/8" and 3/16" printed opposite eachother. The one readable right side up is the correct size. Only need 3 or 4 at this point. Someday we might just have 1 rack that's 3/16, and the other 2 are 1/8". But this isn't a major problem. People will figure it out when their rockets don't fit. We could also mark it on the board somehow.
We're also gonna need to re-label the magnet clips on the board!
Any chance the hot pie plate will melt the gimbals?
Nothing is perfect, but the racks seem pretty good. The pie plates need to be upside down. Charlie's concerns are valid, but we can work out or around most of them once they are in service. I do foresee using some clothes pins now and then for various reasons, but we'll see once they are in service. The bones are nice, but they get lost and occasionally just don't fit the situation.
Are the numbers already printed on the controller? We could keep the colors and still number them 1-6 red, 7-12 blue, 13-18 green, etc. But if the etching included numbers already, I wouldn't feel the need to say the color every time. I'd say something like "Moving to the blue rack, on 1, 2, 3..."
For rod size, could we add a label somewhere on the back side of the rack? A rotating disk with 1/8" and 3/16" printed opposite eachother. The one readable right side up is the correct size. Only need 3 or 4 at this point. Someday we might just have 1 rack that's 3/16, and the other 2 are 1/8". But this isn't a major problem. People will figure it out when their rockets don't fit. We could also mark it on the board somehow.
We're also gonna need to re-label the magnet clips on the board!
Any chance the hot pie plate will melt the gimbals?

Quote from Admin on December 9, 2024, 8:54 amQuote from Eric Becher on December 8, 2024, 8:22 pmNothing is perfect, but the racks seem pretty good. The pie plates need to be upside down. Charlie's concerns are valid, but we can work out or around most of them once they are in service. I do foresee using some clothes pins now and then for various reasons, but we'll see once they are in service. The bones are nice, but they get lost and occasionally just don't fit the situation.
I don't understand this pie plates upside down. The purpose of a launch deflector is to divert and or protect the launch pad from motor exhaust. Little Estes plastic pads use a flat plate to deflect the exhaust from the plastic parts. Those with the small ceramic domes, cause the local exhaust to be deflected outward too. My rail pad uses 11ga. steel at 45º angle to deflect exhaust outward. See its function in this image:
The deflectors' purpose is to keep the exhaust from filthying the rack and or charring it.
Are the numbers already printed on the controller? We could keep the colors and still number them 1-6 red, 7-12 blue, 13-18 green, etc. But if the etching included numbers already, I wouldn't feel the need to say the color every time. I'd say something like "Moving to the blue rack, on 1, 2, 3..."
The launch controller is as seen in the launch controller thread. I really don't see the issue here. At large events, there's typically the A rack (1/8th inch and 3/16th inch) rods numbered 1, 2, 3, ... then the B racks typically 1010 rails numbered 1, 2, 3, ... then the C racks typically 1515 rails numbered 1, 2, 3, ... and then, the away cells typically typically unistrut and numbered 1, 2, 3, ...
MDRA sets up two staging areas — RED and BLACK.
For rod size, could we add a label somewhere on the back side of the rack? A rotating disk with 1/8" and 3/16" printed opposite eachother. The one readable right side up is the correct size. Only need 3 or 4 at this point. Someday we might just have 1 rack that's 3/16, and the other 2 are 1/8". But this isn't a major problem. People will figure it out when their rockets don't fit. We could also mark it on the board somehow.
Yes, I've already considered that.
We're also gonna need to re-label the magnet clips on the board!
If that's a great concern, I could sell my racks to another club.
Any chance the hot pie plate will melt the gimbals?
Do the Estes pads melt under their thin metal blast deflectors? There's a huge difference between temperature (ºF|ºC) and heat (Joules).
Quote from Eric Becher on December 8, 2024, 8:22 pmNothing is perfect, but the racks seem pretty good. The pie plates need to be upside down. Charlie's concerns are valid, but we can work out or around most of them once they are in service. I do foresee using some clothes pins now and then for various reasons, but we'll see once they are in service. The bones are nice, but they get lost and occasionally just don't fit the situation.
I don't understand this pie plates upside down. The purpose of a launch deflector is to divert and or protect the launch pad from motor exhaust. Little Estes plastic pads use a flat plate to deflect the exhaust from the plastic parts. Those with the small ceramic domes, cause the local exhaust to be deflected outward too. My rail pad uses 11ga. steel at 45º angle to deflect exhaust outward. See its function in this image:
The deflectors' purpose is to keep the exhaust from filthying the rack and or charring it.
Are the numbers already printed on the controller? We could keep the colors and still number them 1-6 red, 7-12 blue, 13-18 green, etc. But if the etching included numbers already, I wouldn't feel the need to say the color every time. I'd say something like "Moving to the blue rack, on 1, 2, 3..."
The launch controller is as seen in the launch controller thread. I really don't see the issue here. At large events, there's typically the A rack (1/8th inch and 3/16th inch) rods numbered 1, 2, 3, ... then the B racks typically 1010 rails numbered 1, 2, 3, ... then the C racks typically 1515 rails numbered 1, 2, 3, ... and then, the away cells typically typically unistrut and numbered 1, 2, 3, ...
MDRA sets up two staging areas — RED and BLACK.
For rod size, could we add a label somewhere on the back side of the rack? A rotating disk with 1/8" and 3/16" printed opposite eachother. The one readable right side up is the correct size. Only need 3 or 4 at this point. Someday we might just have 1 rack that's 3/16, and the other 2 are 1/8". But this isn't a major problem. People will figure it out when their rockets don't fit. We could also mark it on the board somehow.
Yes, I've already considered that.
We're also gonna need to re-label the magnet clips on the board!
If that's a great concern, I could sell my racks to another club.
Any chance the hot pie plate will melt the gimbals?
Do the Estes pads melt under their thin metal blast deflectors? There's a huge difference between temperature (ºF|ºC) and heat (Joules).
Uploaded files:
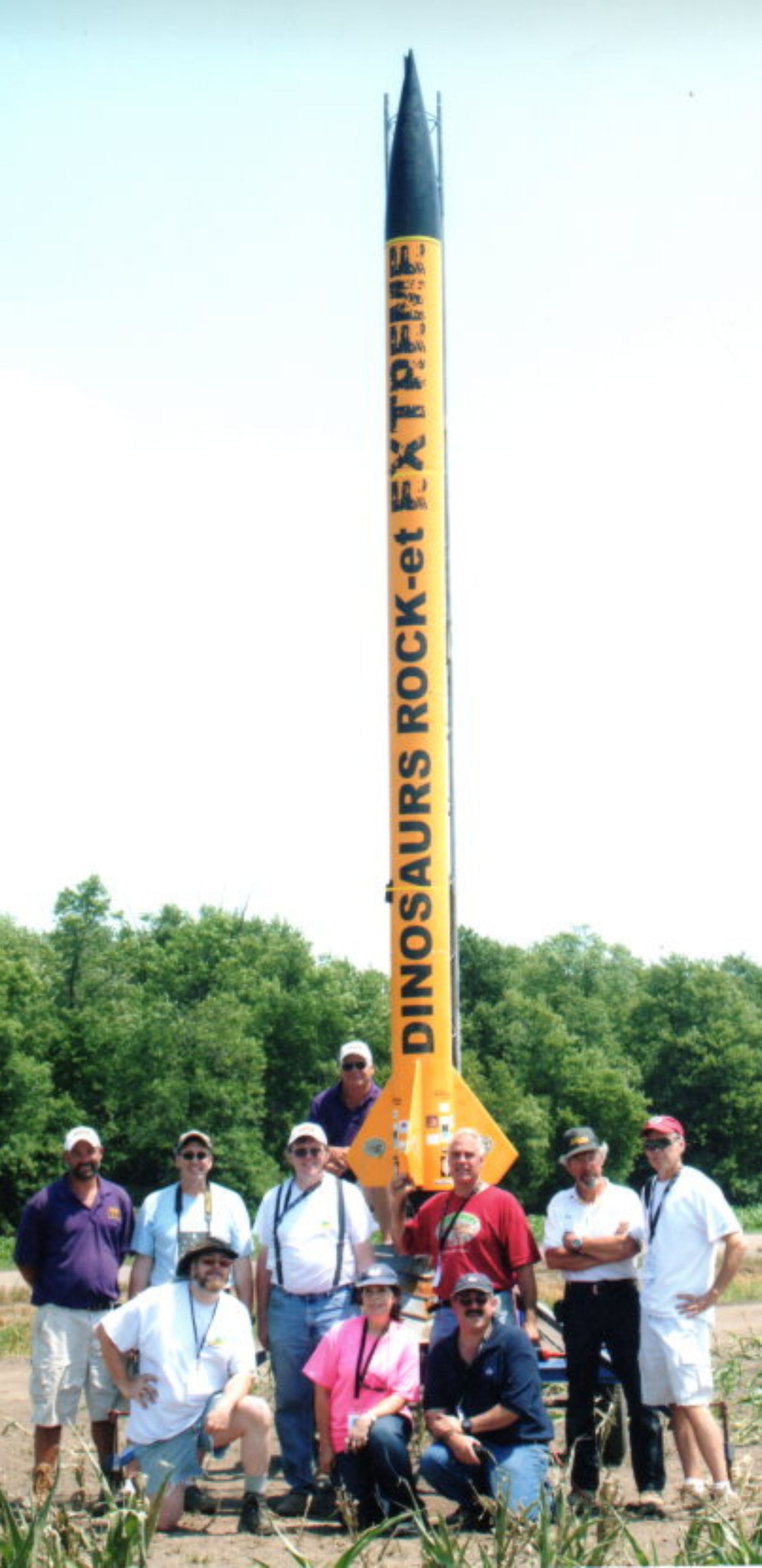
Quote from NeilBrown on December 9, 2024, 9:17 amThe new launch pads look great. Don't get rid of the older ones as if enough people show up they can be used for ARC Teams and/or Civil Air Patrol while the "Club" has use of the newer pads or vice versa - whatever you choose.
The new launch pads look great. Don't get rid of the older ones as if enough people show up they can be used for ARC Teams and/or Civil Air Patrol while the "Club" has use of the newer pads or vice versa - whatever you choose.

Quote from Eric Becher on December 9, 2024, 9:26 amQuote from Admin on December 9, 2024, 8:54 amQuote from Eric Becher on December 8, 2024, 8:22 pmNothing is perfect, but the racks seem pretty good. The pie plates need to be upside down. Charlie's concerns are valid, but we can work out or around most of them once they are in service. I do foresee using some clothes pins now and then for various reasons, but we'll see once they are in service. The bones are nice, but they get lost and occasionally just don't fit the situation.
I don't understand this pie plates upside down. The purpose of a launch deflector is to divert and or protect the launch pad from motor exhaust. Little Estes plastic pads use a flat plate to deflect the exhaust from the plastic parts.
The plates are not flat. The way you have displayed it, they are not angled downward. They are upward cupped near the edges. All we have suggested is flipping them over so they aren't cupped upward, but downward. But it's not that severe. We can try it cupped upward and see what happens.
Please note that we have not said we don't want them, or that they are not an improvement. We're just thinking about ways they will be used and what adjustments we will have to make in how we operate to make implementation smooth. You can't have clips numbered one way and the racks numbered another. It confuses people. So we change the clips. No big deal. But it should be done before the second one, or the controller is put into use.
Quote from Admin on December 9, 2024, 8:54 amQuote from Eric Becher on December 8, 2024, 8:22 pmNothing is perfect, but the racks seem pretty good. The pie plates need to be upside down. Charlie's concerns are valid, but we can work out or around most of them once they are in service. I do foresee using some clothes pins now and then for various reasons, but we'll see once they are in service. The bones are nice, but they get lost and occasionally just don't fit the situation.
I don't understand this pie plates upside down. The purpose of a launch deflector is to divert and or protect the launch pad from motor exhaust. Little Estes plastic pads use a flat plate to deflect the exhaust from the plastic parts.
The plates are not flat. The way you have displayed it, they are not angled downward. They are upward cupped near the edges. All we have suggested is flipping them over so they aren't cupped upward, but downward. But it's not that severe. We can try it cupped upward and see what happens.
Please note that we have not said we don't want them, or that they are not an improvement. We're just thinking about ways they will be used and what adjustments we will have to make in how we operate to make implementation smooth. You can't have clips numbered one way and the racks numbered another. It confuses people. So we change the clips. No big deal. But it should be done before the second one, or the controller is put into use.